The Importance of Non-Magnetic Connectors in MRI Applications
The advancement of MRI machines focuses on increasing resolution and magnetic field strength, and hinges on the quality of non-magnetic connectors. - Ketan Thakkar - Sr. Product Manager
Download PDFMRI advancements focus on increasing the resolution of MRI scans and increasing MRI machine magnetic field strength. Both of these enhancements hinge on the quality of non-magnetic RF connectors used to carry RF pulses and sense the incredibly weak signals returned by magnetically realigning protons. Greater resolution and higher-power MRI require more, and denser, RF interconnect than previous MRI technologies, creating new design challenges in designing, manufacturing, and maintaining MRI machines.
Why MRI Machines are Dependent on Non-Magnetic RF Connectors
The overall benefits of magnetic resonance imaging (MRI) over other imaging techniques have spawned competition and advancement of MRI technologies, as well as new medical devices designed to be compatible with MRI use. While there are established uses for MRI in areas such as neurology, there is a growing use of MRI within the medical community for new applications, such as magnetic resonance angiography (MRA) and cardiac MRI (CMRI). Hence, there is a growing focus in developing more advanced MRI technology to serve existing applications and enable new use cases.
MRI advancements focus on increasing the resolution of MRI scans and increasing MRI machine magnetic field strength. There is currently research and studies being conducted to develop much higher magnetic field strength MRI machines, which could lead to a transition from the 1.5 to 3 Tesla MRI seen today, to 7 Tesla or even over 10 Tesla MRI. Both of these enhancements hinge on the quality of non-magnetic RF connectors used to carry RF pulses and sense the incredibly weak signals returned by magnetically realigning protons. Greater resolution and higher-power MRI require more, and denser, RF interconnect than previous MRI technologies, creating new design challenges in designing, manufacturing, and maintaining MRI machines.
This article strives to educate MRI manufacturers and industry professionals on the relevant trends with MRI technology and how these trends impact the use of RF interconnect in MRI machines. This article will also touch on the use of non-traditional MRI applications and the growing demand for non-magnetic RF interconnect for implantable medical devices.
MRI/MRA Interconnect Obstacles?
Current MRI machines use many RF connectors, contacts, and cables to send and receive the pulsed RF signals used to image patients. If these connectors, contacts, or coils contain any ferromagnetic material, from impurities or by design, the magnetic field response from the patient can be altered. Any alteration of the signal reduces MRI accuracy. Hence, MRI machines are typically now made with non-magnetic RF interconnect and contacts, which are tested to ensure they yield no magnetic response.
Non-Magnetic Connector Solutions
View the CatalogThough using non-magnetic RF connectors and contacts enables higher-resolution MRI, new MRI advances are leading to additional RF interconnect challenges beyond needing merely non-magnetic connectors. To further enhance the resolution and the signal-to-noise ratio (SNR) of an MRI scanner, much higher magnetic field strengths are used. Even with higher-Tesla MRI machines, to take advantage of higher spatial resolution technology, the RF receiver and RF path must introduce as little loss and distortion as possible. Moreover, there are new studies and research on different MRI probe typologies that use an array of magnetic field probes instead of conventional surface coils. These new types of magnetic probe MRI could lead to much higher-resolution MRI but would also require a greater number of RF interconnect and signal processing circuitry.
Denser RF interconnect means that there will likely be a greater need for board-launch, end-launch, and ganged board-to-board RF connectors, in addition to commonly used non-magnetic RF cable assemblies. Given that the majority of suppliers offering RF interconnect have a relatively limited selection of non-magnetic RF solutions compared to standard RF interconnect, MRI manufacturers are often limited in their options for reducing the size and complexity of their MRI design. There may also be nebulous search results if an MRI manufacturer desires high-quality and reliable non-magnetic RF interconnect. This is not the case with Cinch’s Johnson™ RF connectors, which features the broadest portfolio of non-magnetic RF connectors in the industry.
Uses of Non-magnetic RF Interconnect for Medical Applications
There is a trade-off with RF interconnect related to size, frequency, power handling, and insertion loss. Typically, smaller RF connectors are able to channel higher frequencies, but at the cost of lower maximum power handling and increased insertion loss. Special design techniques and materials can be used to mitigate the insertion loss of using smaller RF interconnect and thus enable much smaller RF connections. Though not universally available from every vendor, there is a range of non-magnetic RF connector types used with MRI, mainly N-type, SMA, BNC, SMB, SMC, MCX, MMCX, SMP, SMPM, and 2.92 mm. The type of connector used depends on the frequency, signal power, geometry at the connection point, insertion loss considerations, and installation dynamics.
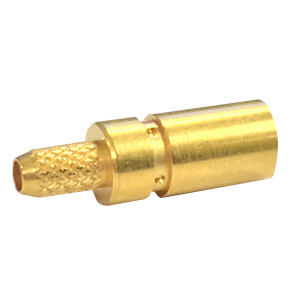
MCX Non-Magnetic Jack133-9303-001
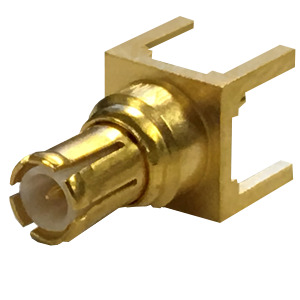
MCX Non-Magnetic Plug133-9801-201
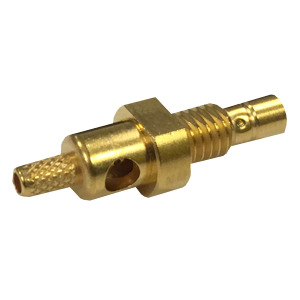
SMB Non-Magnetic Jack, RG316131-9303-401
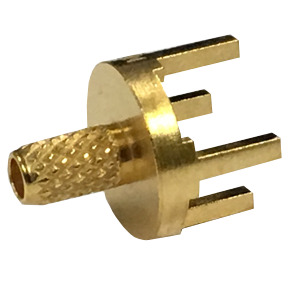
SMB Non-Magnetic Jack, RG188142-9003-201
These types of connectors also come in a range of configurations, including end-launch, right-angle, straight, bulkhead, and surface mount receptacles. The connector configuration used in a particular connection depends on the geometric requirements of that connection and how the cable, or board connector, is to be installed. With a greater number of RF probes or magnetic coils in an MRI, more board-mount RF connectors are likely to mitigate the potential footprint increase that additional RF sensors would contribute to the MRI machine. There are relatively limited physical dimensions on the patient housing area and the overall size of an MRI machine, with a need for the superconducting magnet and MRI probes to be as close to the patient as possible. Using much smaller and intelligently configured board-mount non-magnetic RF connectors could enable the development of much more compact MRI machines.
Typical RF connectors are threaded bodies that require precise torque values, and hence torque wrenches, to properly install. There are also snap-on, push-in, or blind-mate style connectors. These types of connectors are designed to make a secure mechanical and electrical connection from merely being pressed together with adequate force. Blind-mate connectors also exhibit resistance to misalignments during mating, and depending on the connector design, may include sophisticated self-aligning features. This is crucial during assembly, installation, and maintenance.
There is also a growing interest in using MRI for more applications, including cardiac imaging and magnetic-resonance angiography (MRA). Though legacy implants with ferromagnetic materials, such as stents or pacemakers, would make using an MRI machine impossible with these patients, there are a growing number of implantable medical devices that are intentionally using non-magnetic components to allow for higher-resolution MRI scans instead of typical CT or SPECT scans. There is also a trend of using wireless connectivity instead of wired connectivity to access, control, and monitor features of implanted medical electronics. For implanted medical devices using wireless technologies to be MRI compatible, they require non-magnetic RF interconnects. As these fields and applications grow, there may be increased use of non-magnetic RF interconnect with implantable medical electronics.
Lastly, using a trusted vendor with a diverse range of non-magnetic RF connectors can also be beneficial during design, production, and throughout the lifetime of an MRI machine. High-quality RF connectors could yield better-performing MRI machines with greater reliability and lower production costs, compared to lower-quality connectors that may have magnetic impurities, suffer from reliability issues, or are difficult to source.
To ensure Cinch’s customers receive the highest quality and lowest Mμ connectors possible, JohnsonTM brand of non-magnetic RF interconnect undergo rigorous screening for components and assemblies. This is a substantial added value, as JohnsonTM features the largest variety of non-mag MRI interconnect solutions available.
Explore Bel's Variety of Non-Magnetic Coax Connectors
Johnson, a product line of Cinch Connectivity Solutions, has expanded the connector product groups in its popular line of Non-Magnetic RF coaxial connectors and cable assemblies. MCX and MMCX micro-miniature connectors have been added to satisfy the needs of the RF coil manufacturers that are building smaller coils for MRI equipment. Customized flex coils and array coils can image smaller parts of the body such as wrists, feet, hands and other appendages.
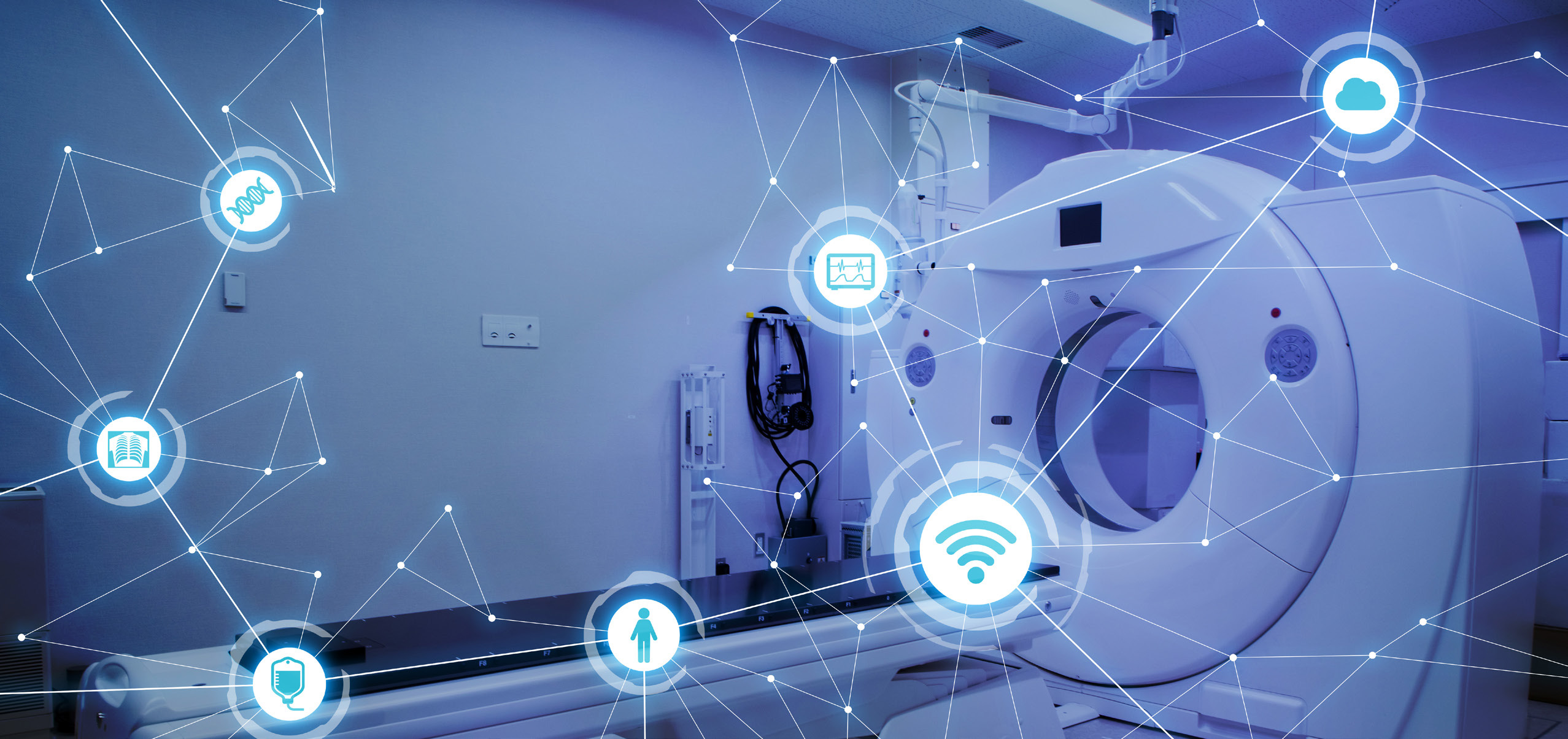
View Johnson's Full Line of Non-Magnetic Coax Connectors
Learn More