Transformer Basics: Insulation Systems and Material Choices
Explore transformer basics with a focus on insulation systems, coil winding, core types and compliance considerations. Gain insights for optimizing performance.
Download PDFIn this guide, we cover the fundamental aspects of transformers, focusing on insulation and material choices. Learn about insulation systems, coil winding methods, and various core types. Gain insights into the crucial design considerations that engineers and manufacturers grapple with to optimize transformer performance.
PART I: UNDERSTANDING INSULATION TYPES
To those unfamiliar with transformer manufacturing, terms such as fish, kraft, natural fiber and gum might sound like the main ingredients for Fish Provencale. But to those in the know, these terms simply define the type of sheet insulation used in the transformer manufacturing process. Kraft paper, fish paper (vulcanized fiber), Nomex®, and Mylar® are some of the sheet film insulation materials commonly used in the manufacture of layer-wound transformer coils.
LAYER-WOUND COILS
A layer-wound coil consists of single layers of wire separated by layers of insulation. Here, the insulation serves a dual purpose: it is a support platform for the wire and electrical isolation from parts having opposite polarity and other conductive materials (i.e., core, other windings).
BOBBIN-WOUND COILS
For transformers with power ratings less than 1 kVA, manufacturing trends tend to favor bobbin-wound coils. A bobbin-wound coil consists of layers of wire precision-wound on a rigid form. The rigid form, or bobbin, is the support platform and electrical isolation for the windings. Bobbin forms are commonly molded from thermoset materials such as Rynite®, Zytel®, Ryton®, and others.
The major reasons for the growing popularity of bobbin-wound transformers are:
- Reduced labor costs
- Reduced manufacturing time
- Design simplification
- Reduced size and weight
Bobbin wound transformers rely primarily on thin film tape insulation rather than sheet insulation to provide separation and isolation between groups of windings.
Another important advantage of multi cavity bobbin-type construction is the fact spacing accuracy is virtually guaranteed during the manufacturing process. Bobbin coils can be manufactured at much higher production rates with less attention to intricate winding and insulation techniques. This is especially important for transformers utilized in products sold worldwide.
Table 1. Maximum Acceptable Temperature Rise (°C) for windings protected inherently.
System Class | Under Abnormal Conditions* |
105 (A) | 150 |
120 (E) | 165 |
130 (B) | 175 |
155 (F) | 190 |
180 (H) | 210 |
Date per IEC/EN 61558-1-2 standard. |
Layer-wound coils require accurate placement of conductors, insulation material and anchor tapes to maintain spacing and insulation barriers. More labor-intensive to build, layer wound coils require manufacturing processes that are more susceptible to deviation during winding.
U.S. manufacturers must look offshore for bobbins forms large and strong enough to support transformers greater than 1 kVA. Most large bobbins molded in the U.S. do not have sufficient wall thickness and lack the rigid support for the larger conductors used in the manufacture of >1 KVA transformers.
IMPORTANCE OF INSULATION SYSTEMS
All transformers, whether layer-wound or bobbin-wound, benefit from the use of approved insulation systems suitable for the user's application. A transformer with an inadequate insulation system can be a potential fire and shock hazard. Table 1 lists insulation temperature class ratings and the maximum allowable temperature under abnormal conditions.
An interesting fact relevant to Underwriters Laboratories, (UL) Recognized insulations systems is; some Class A materials may be used in higher class ratings when impregnated with a suitable varnish. Hydroscopic materials such as Kraft paper will take on the characteristics and rating of a higher insulation system rating when impregnated with a suitable recognized insulating varnish.
Regardless of the system required, users of transformers should verify transformers purchase incorporate recognized insulation systems UL Recognized insulation systems have materials that have been proven to be compatible with each other for a specific temperature range. With this type system, the user can be assured that the transformer can withstand the temperature levels for which it has been designed. Most reputable transformer manufacturers offer several insulation systems. Recognized insulation systems are typically listed on UL’s data base.
Nomex, Mylar, Rynite, and Zytel are DuPont trade names.
Ryton is a Philips trade nam
Table 2. Maximum Acceptable Temperature Rise (°C) for windings protected inherently.
Insulation Guide |
||||
Insulations & Typical Trade Name |
Thermal Rating |
Nema NW 1000 |
Federal Spec. |
Mil W 683C Class/Type |
Plain Enamel Polyurethane Polyurethane Bond Formvar Formvar Bond Poly-Nylon Bond |
105°C |
MW 1-C MW 2-C MW 3-C MW 15-C MW 19-C MW 29-C |
JW 1177/1 JW 117/2 JW 1177/4 JW 1177/6 |
Class 105 Types T thru T-4 |
Polyurethane Nylon-Poly H.T. |
103°C |
MW 28-C MW 75-C |
JW 1177/9 |
Class 130 Types B thru B-4 |
Polyester Polyester Epoxy Bond |
155°C |
MW 5-C |
JW 1177/10 |
Class 155 Types L thru L-4 |
Polyester/ Polymide Isomid* Polyester Nylon Solderable Polyester Solderable Polyester Nylon |
180°C |
MW 30-C MW 30-C MW 24-C MW 26-C MW 27-C |
JW 1177/12 JW 1177/12 JW 1177/11 |
Class 180 Types H thru H-4 |
Armored Polyester Teflon* |
200°C |
MW 36-C |
JW 1177/14 |
Class 200 Types K thru K-4 |
ML* |
220°C |
MW 16-C |
JW 1177/16 |
Class 220 Types M thru M-4 |
PART II: TOROIDAL VS LAMINATED CONSTRUCTION
Tradeoffs associated with the selection of EI laminated or tape-wound toroidal cores include cost, circuit application, weight efficiency, shape and volume.
Power transformers are available in a variety of configurations, primarily determined by the type of core selected. For the most part, they boil down to one of two types: EI laminations and tape- wound toroidal cores. The tradeoffs involved in selecting one over the other usually include cost, circuit application, weight, efficiency, shape and volume. The basic electrical function between the two transformer types referenced is the same: one or more electrically conducting coils coupled together through magnetic induction.
Core selection has the greatest effect on transformer size and volume. EI laminations and tape- wound toroidal cores, though available in the same materials exemplify these Inherent to the toroidal transformer’s construction, the winding occupies the full periphery of the core, resulting in reduced leakage inductance and stray magnetic fields, as well as reduced audible hum.
TOROIDAL CORES
The carbon steel foil used in the construction of toroidal cores is usually thinner than the commonly-used lamination plates (toroid core foils are usually 9 or 11 mils thick, as opposed to lamination plate thickness of 14 mils or 18 mils. This thickness reduction in part permits the transformer to be operated at higher influx densities without undue increase in core loss and magnetization currents.
The effective air gap in toroidal cores is significantly lower than that of interleaved EI cores which results in a higher stacking factor (0.95 vs 0.90) and improved volumetric efficiency.
Toroidal cores do not require a polymeric bobbin form, making more window room available for magnet wire. The disadvantage associated with toroidal transformers is price. The nature of a toroidal core necessitates slower, more complex winding techniques, particularly for high voltage or multi-output transformers where many wire changes or many turns are required. The more labor intensive construction typically demands a higher selling price. In addition, the level of isolation required to meet safety agency requirements is easier to achieve with multi cavity bobbin wound EI laminated transformers.
Due to the advantages of lower cost off shore labor, the price differential between toroid and EI laminated transformers is shrinking.
EI LAMINATED CORES
Transformers exceeding approximately 1500 VA offer improved stacking factor ratios. The result of reduced effective air gap and core geometry of toroidal transformers most often results in excessive inrush current. Inversely most EI laminations offer lower inrush current. Further in-rush current reduction may be achieved by the introduction of an air gap in the core’s construction. Reducing the in-rush current on toroidal transformers is far more difficult and expensive. It sometimes becomes necessary to add delay modules in series with a primary of a toroidal transformer to prevent destruction of overload protectors on turn-on.
There are ways of minimizing the disadvantages of laminated construction. The detrimental effects of stray magnetic fields and induced hum can be reduced by locating the transformer as far away from sensitive areas as possible, rotating the transformer so that magnetic fields are perpendicular to one another, or via magnetic shielding. Mechanical hum within the transformer can be reduced with a quality impregnation/potting system (i.e., vacuum impregnation and/or overpressure).
Stray field emissions can be reduced by using UI type laminated cores. This structure, often called hum-bucking or semi toroidal, uses opposing fields in opposite legs of the core to cancel one another. Signal's LP and IF series are built this way.
Due to the size constraint limitations of toroidal cores, the majority of the world’s power transformers are built with EI laminations.
Design engineers, recognizing the price advantage of standard, off-the-shelf EI laminated transformers and reserve the use of toroidal transformers where the size and weight benefits outweigh availability and price
PART III: TRANSITIONING TO IEC/EN 60950
National, regional and international transformer requirements and specific applications require the system manufacturer to be aware of the end product standards.
The Safety Agency such as UL, CSA, and VDE are quite familiar to most compliance engineers of manufacturing facilities. Also well known is the International Electrotechnical Commission or IEC. The IEC is a standards writing body supported by a vast network of National Committee delegates, most having technical expertise.
Figure 1: Signal IF Transformers
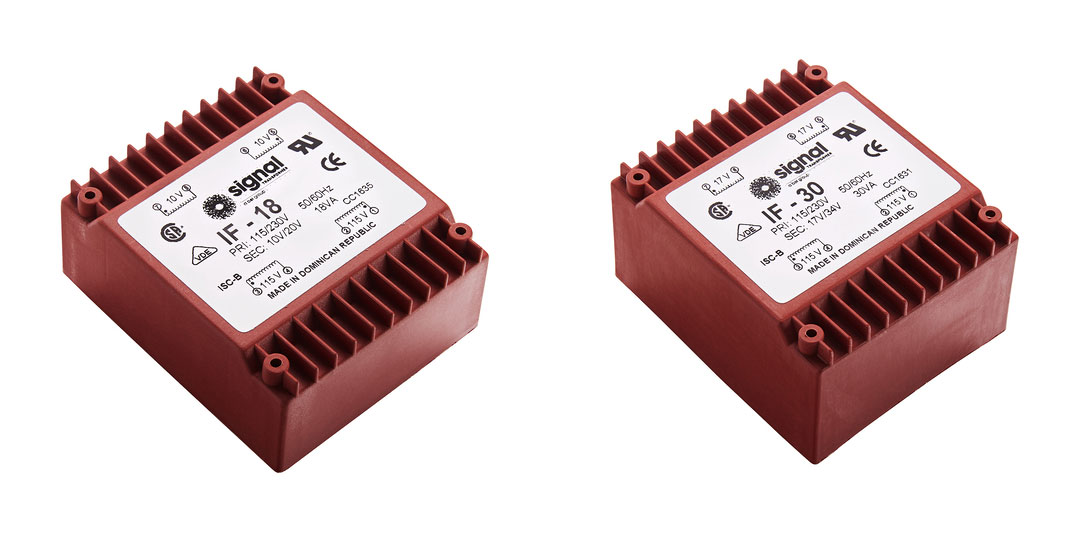
The IEC 60950 and the European Normative, (EN) version consolidates the requirements in the former IEC 380 (Safety of Electrically Energized Office Machines) and the IEC 435 (Safety Data Processing Equipment). This standard is embodied in several other national and regional standards, including UL 601950 (U.S.), VDE 0805, Part 100 (Germany), BS 16204 (U.K.) and the CSA C22.2950 (Canada). In general, the Many end product manufacturers find that component recognition to UL’s and CSA’s general purpose transformer standards is acceptable. The transformer standards UL 506 (U.S.), CSA 22.2 no. 66 1988, (largely considered general purpose transformer standards), are soon to be replaced by the recently published UL 5085 parts 1, 2 and 3. UL’s 1585 standard for Class 2 and Class 3 transformers will also be replaced by the UL 5085.
Germany’s premier test house; VDE still utilizes the transformer standards 0550/0551, (based on the IEC 60742), for some special applications however, the IEC / EN 61558-1 is the predominant standard in use. Most of Signal’s off-the-shelf transformers are UL recognized, CSA, VDE and or TUV certified. Please refer to our product listing for specific recognition / certification marks.
Harmonization efforts in the US and Canada of the IEC standards; 60950, (Information Data Processing Equipment), and IEC 60601 (Electro Medical Equipment), are largely completed. The same cannot be said for the IEC transformer standard IEC 61558-1-2.
UL has not begun harmonization efforts with this standard and are not likely to do so in the near future. Signal’s engineering staff has the regulatory experience to design transformers to meet both North American and International standards.
In the U.S., some regional areas have their own requirements. For example, the City of Los Angeles, CA, situated on an active geological fault zone, has established requirements certain for transformers that are more stringent than UL’s general standards, e.g. requirements for tamper-proof, thermal protection and nonflammable materials.
AWG AND MAGNETIC WIRE DIAMETER
Magnetic wire is an important part of nearly every transformer. Whether wound on bobbin forms or layer wound, proper selection and care of magnetic wire in the design and manufacturing process helps ensure that the final product will perform as designed.
Magnet wire is typically a solid copper conductor, circular in cross-section, coated with one or more layers of insulating polymer. The wire is available in a range of conductor diameters, specified as AWG (American Wire Gauge). We normally use gauges that range from 8 to 44 AWG. The AWG number is related to cross-sectional area by the formula:
A = 2
where:
g = AWG number
A = Cross-sectional area in circular mils (a circular mil is the area of a circle 0.001 in. in diameter).
Resistance of a length of a wire, and therefore its power dissipation, is inversely proportional to its cross-sectional area. Thus, transformer design is a tradeoff between wire size and power dissipation. Equivalently, it is a tradeoff between size and regulation.
Depending on the application, the magnet wire’s insulating coating may be comprised of a single layer of polyurethane, or multiple layers of polyurethane and additional nylon polymer overcoat. In critical applications requiring high abrasion resistance or an extended temperature rating, the multi layer wire is used.
An important practical characteristic of magnet wire is its solderability; for use in mass production, the magnet wire’s insulation must be removable in a solder bath at. An additional characteristic of the insulation coating is dielectric break-down voltage and Not all transformers are wound exclusively with round AWG magnet wire. In high current applications, foil or wire of square or rectangular cross-section may be used. For high frequency power work, where skin effect can cause significant losses, either foil or litz wire, (multi stranded, twisted insulated wire), is used. And for transformers that will see extreme environmental conditions, high temperature wires are available
ENSURING COMPLIANCE WITH TRANSFORMER STANDARDS
The ability to navigate the complex landscape of national and international transformer standards is essential for manufacturers aiming to ensure compliance and safety. While harmonization efforts for standards like IEC 60950 and IEC 60601 are largely completed, IEC 61558-1-2 remains less unified. As the industry continues to evolve, staying informed about regional and international requirements will be crucial for maintaining product excellence and compliance. Signal’s engineering team is wellequipped to design transformers that meet both North American and international standards, reducing the burden on engineers
Discover how Signal can support your projects and ensure compliance by connecting with our expert team.
Learn More